How can we organise visual management with digital indicators?
Visual management allows you to know whether the situation is normal or abnormal for an activity zone. The purpose is to rapidly visualise relevant indicators of a department or shop floor to be able to manage the different activities efficiently. Updates of these visual management boards requires a lot of data to constantly update and lots of time and energy.
How do you structure visual management with rapid, fluid and reactive indicators?
SESA SYSTEMS innovation in 2020 stems from the creation of the SESAHUB platform, which is used to combine all flows which are exchanged in real-time with production operators. Gathering production line data on SESAHUB helps display production monitoring indicators and other indicators in real-time. This digital visual management at production sites is carried out via digital screens linked to an internal or external network. SESAHUB structures and organises an instant and ongoing communication and exchange network, production meetings are coordinated with a chain of interactive screens: E-STATION, E-LEANBOARD, E-MEETING and E-ACTIVBOARD.
This digital visual management provides rapid access to company data for shared, efficient and rapid decision-making.
Deployment of Visual Management
Successfully sharing corporate strategy with significant involvement by managers and dynamically deploying through its organisation is a crucial issue for management. Management is responsible for the company vision, defining objectives and the action strategy. It will associate each of these actions with performance indicators. These indicators must be representative of the expected results. Whilst the communication system in place helps convey missions, values and objectives, the means and methods put in place, it is important to also convey the elements which have meaning for company employees, like real-time results. In this way, employees, regardless of seniority, can use plans, assess and respond depending on the results obtained as part of a continuous improvement process.
Progress is assessed and problems corrected. Operators record their results every hour (production, interventions, scrap, etc.). Deviations are identified more easily and can be managed immediately. Every day, Team Leaders organise a meeting (TOP 5’) The results from the previous day are reviewed. The working day is organised depending on these results. Department leaders organise a meeting on Monday morning and review figures from the previous week. Finally, every month, the dashboard is updated and discussed during the management committee. It is used to verify that the results comply with the expected objectives and to implement new actions which will be deployed, where applicable.
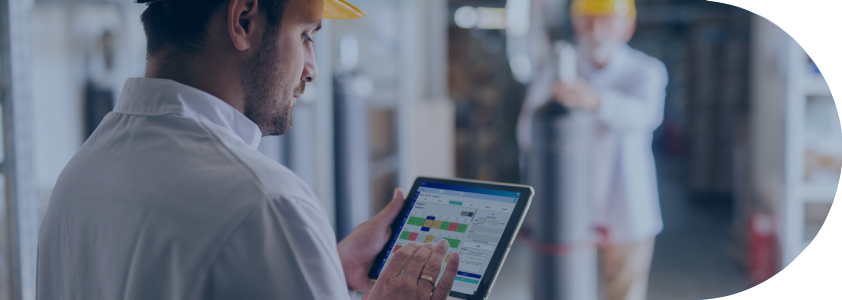
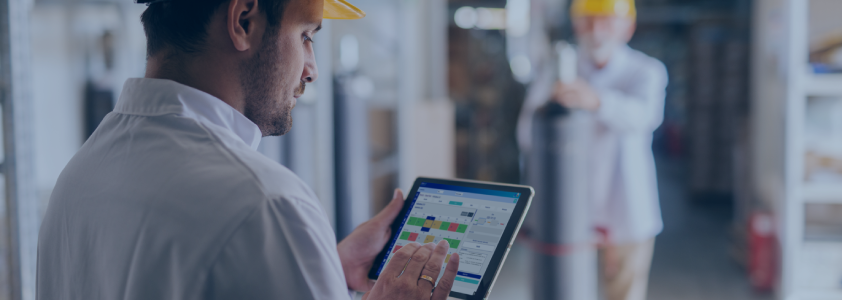